In de MXGP is het intussen gemeengoed geworden: een fancy gekleurde coating op de vorkpoten van de fabrieksmachines. Amateur-rijders die er geld willen tegenaan smijten kunnen beschikken over dezelfde technologie. Alle motoren komen standaard uit de fabriek met glanzend chromen vorken maar is een andere coating dan zoveel beter? Is het een modeverschijnsel of werken die dure coatings echt wel?
Waarom gebruiken de fabrikanten standaard chroom op hun vorkpoten?
Het antwoord is heel eenvoudig: de kostprijs. Het aanbrengen van chroom op staal is een relatief goedkoop proces in vergelijking met complexere procedures die worden gebruikt voor titaniumoxide (TiO2), titaniumnitride (TiN) en diamantachtige coatings (DLC). Het aanbrengen van chroom gebeurt in vijf stappen.
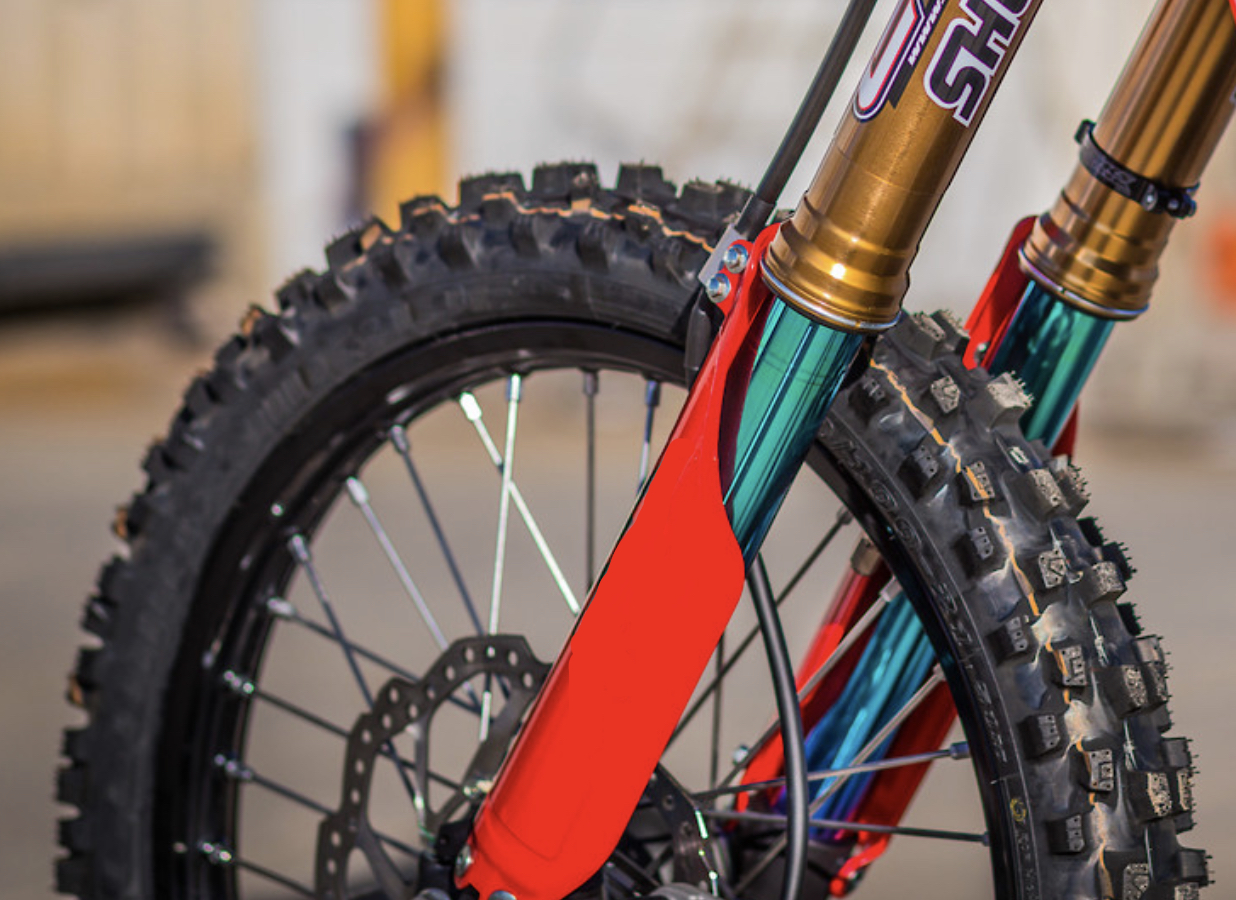
De titaniumoxide coating op een Honda CRF
De stalen buis of tube wordt eerst gereinigd. Dan wordt de buis in een zuur ondergedompeld om het oppervlak te etsen. Hiermee worden onzuiverheden zoals ijzeroxide (roest) chemisch verwijderd. Dan krijgt de stalen buis een negatieve elektrische lading en wordt deze ondergedompeld in een bad met positief geladen chroomhoudende vloeistof. De positief geladen chroomdeeltjes verbinden zich met de negatief geladen buis.
De tube wordt daarna schoon gespoeld en gepolijst voor een gladde afwerking van het oppervlak. Hoe ingewikkeld deze procedure ook klinkt, hij is eigenlijk eenvoudiger en goedkoper dan TiO2, TiN of DLC.
Waarom TiO2, TiN of DLC?
Puur praktisch zijn er waarschijnlijk twee belangrijke gebieden die we willen proberen te verbeteren: de wrijving en de weerstand tegen schade. We kunnen ook proberen het gewicht te verminderen, maar chroomcoating is slechts 0,03 mm dik, dus er valt niet veel te winnen door over te stappen op een ander materiaal. Laten we dan eens kijken naar wrijving.
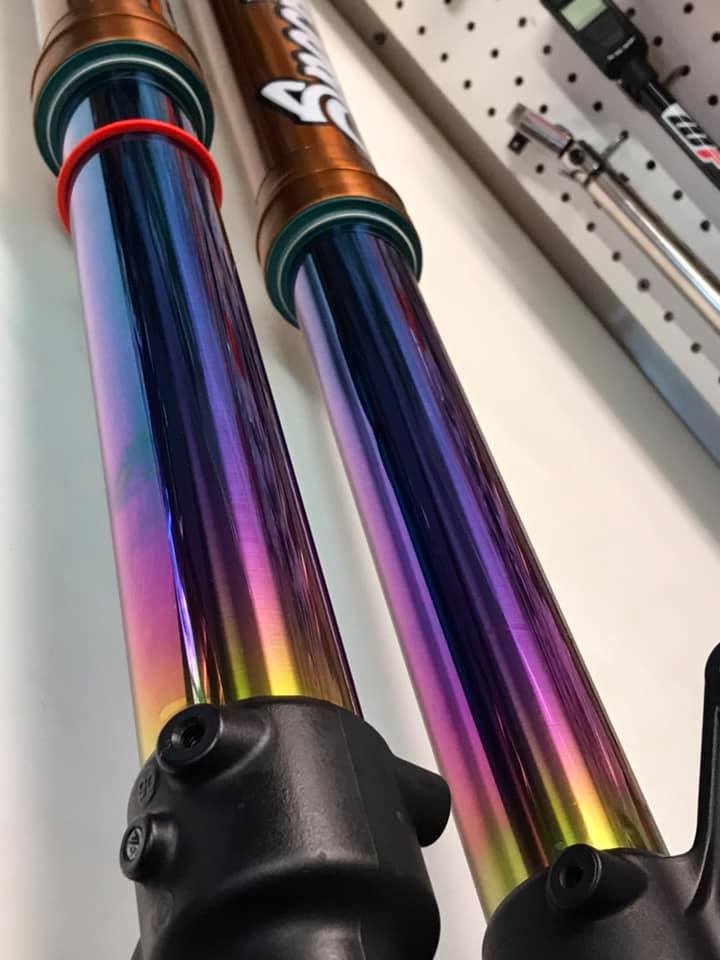
Titaniumnitride coating gecombineerd met buitenpoten behandeld met Kashima coating.
Gelukkig is er een meeteenheid die we hiervoor kunnen gebruiken, het heet het “wrijvingscoëfficiënt” en het vertegenwoordigt de relatie tussen twee krachten. In dit geval is het de kracht die nodig is om een object op een oppervlak te verplaatsen, gedeeld door het gewicht van dat object in Newton. Als je bijvoorbeeld een blok rubber van 1kg (9,81N) op beton hebt liggen en er is een kracht van 5N nodig om het te verplaatsen, dan is de wrijvingscoëfficiënt 0,51. Er zijn zelfs gestandaardiseerde testen om wrijving te meten, één daarvan heet de ASTM G99.
In principe wordt het materiaal met een standaardafmeting op een testbed geplaatst en tegen het bed gedraaid en worden de krachten gemeten. De kracht die nodig is om een object in beweging te brengen vanuit een statische positie is groter dan de kracht die nodig is om een object in beweging te houden, dus de test moet de statische wrijving overwinnen (soms “stiction” genoemd in de motorcrosswereld) en als het materiaal dan beweegt, kunnen we de dynamische wrijving meten.
Nu we weten hoe de test wordt uitgevoerd, zijn hier de waarden:
- Chroom: Statisch: 0,16-0,20. Dynamisch: 0,10-0,20.
- TiO2: Statisch: 0,35-0,40. Dynamisch: 0,30-0,35.
- TiN: Statisch: 0,40-0,55. Dynamisch: 0,30-0,50.
- DLC: Statisch: 0,05-0,20. Dynamisch: 0,05-0,15.
Het lijkt erop dat DLC potentieel heeft, maar waarom zouden we TiO2 of TiN gebruiken als de wrijvingswaarden van chroom lager zijn?
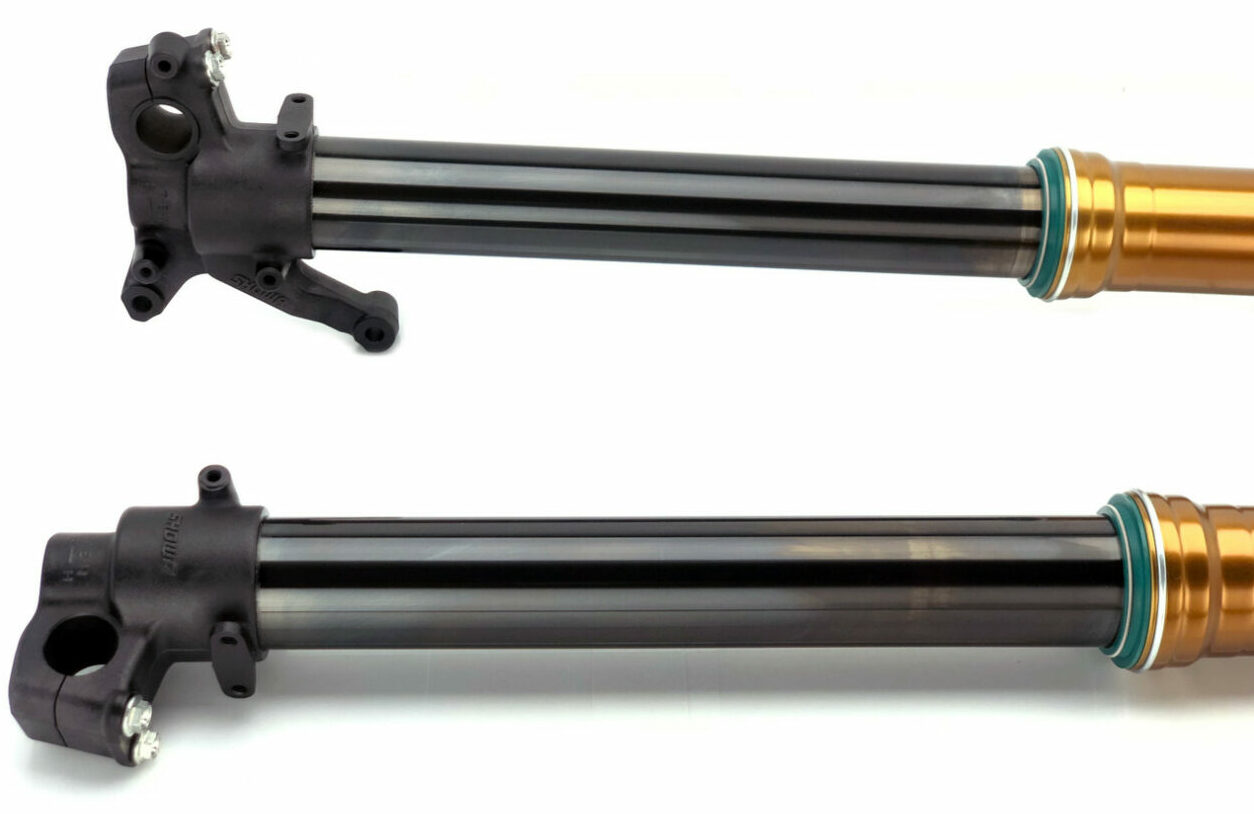
De typische zwarte kleur van DLC-coating
Laten we eens kijken naar de voordelen van TiO2, TiN en DLC ten opzichte van chroom. TiO2 biedt een betere weerstand tegen corrosie. TiN vormt een zeer hard oppervlak en biedt een betere slijtvastheid terwijl DLC een extreem lage wrijving en betere slijtvastheid heeft.
We hebben het nog niet gehad over anodiseren of Kashima coating, en dat komt omdat dit voornamelijk van toepassing is op aluminium en niet op staal. Als we aan aluminium denken, is het weliswaar een heel licht materiaal in vergelijking met staal, maar ook een heel zacht materiaal. Idealiter zouden we de hardheid ervan willen verbeteren, zodat de slijtvastheid wordt verbeterd, en het zou ook fijn zijn om lagere wrijving te hebben als het gaat om ophanging.
Een manier om de hardheid van aluminium te verbeteren is door anodiseren. Anodiseren is vergelijkbaar met verchromen, dit is het proces:
Reinigen, etsen, verwijderen van oxidatie en het anodisatieproces zelf. Het aluminium wordt in een elektrolytisch bad geplaatst, meestal gemaakt van zwavelzuur, chroomzuur of fosforzuur, afhankelijk van de toepassing. Het aluminium fungeert als de anode (positieve elektrode) en een kathode (negatieve elektrode), meestal gemaakt van lood of roestvrij staal, wordt in het bad geplaatst. Een gelijkstroom elektrische stroom wordt door de oplossing geleid. Zuurstofionen uit de elektrolyt verbinden zich met de aluminiumatomen op het oppervlak om aluminiumoxide (Al₂O₃) te vormen.
Het is de oxidelaag die de hardheid van het aluminium verbetert, maar met hoeveel?
Gelukkig is er een andere gestandaardiseerde test die we kunnen gebruiken, de Rockwell hardheidstest. Bij deze test wordt een gereedschap met een diamantpunt in het materiaal gedrukt en de testmachine kan meten hoe ver de punt in het materiaal is gegaan.
De resultaten zijn:
- Onbehandeld aluminium: 15 tot 30 HRB
- Geanodiseerd aluminium: 60 tot 65 HRC
Dit betekent dat het geanodiseerde aluminium 4-5 harder is dan onbehandeld aluminium, geweldig voor de slijtvastheid! Maar hoe zit het met onze oude vriend wrijving? Het antwoord is niet geweldig als de oppervlakken droog zijn, en redelijk als deze gesmeerd zijn:
- CoF’s onbehandeld aluminium: Statisch: 0,3 – 0,45, Dynamisch: 0,2-0,4, Gesmeerd: 0.1-0.2
- Verzegeld geanodiseerd aluminium: Statisch: 0,4-0,7, Dynamisch: 0,3-0,5, Gesmeerd: 0.1-0.25
De oxidelaag die ontstaat tijdens het anodiseren is eigenlijk vrij ruw. En dit is waar de Kashima coating om de hoek komt kijken. Kashima coating is een eigen ontwikkelt anodiseerproces van het bedrijf Miyaki Co. Ltd. in Japan. Waarom het Kashima heet is niet geweten.
Hoe dan ook, het Kashima proces is ontwikkeld om aluminium de verbeterde hardheid van anodiseren te geven en tegelijkertijd de wrijving te verminderen, en dit wordt gedaan door een extra smerende molecuul als onderdeel van het anodiseerproces. Hoe werkt het? Kijk maar eens naar de afbeelding hieronder op de website van Kashima. Het spreekt voor zich dat de Kashima coating alleen gebruikt wordt voor buitenpoten gezien het een procedé is om aluminium te coaten.
Zijn speciale coatings voor je vering de moeite waard?
Zoals gewoonlijk hangt het weer af van je beschikbare budget en/of het niveau waarop je rijdt. Als je een professioneel raceteam bent dat op zoek is naar elke 1% prestatieverbetering, dan zijn binnenpoten met DLC-coating en buitenpoten met Kashima-coating de beste keuze. Als je een gemiddelde amateur-rijder bent, kun je je geld misschien beter besteden aan het onderhouden van je vering of aan het kopen van de juiste veren voor jouw gewicht en vermogen.
Bedankt aan Jens Köpke, CEO van Motoklik, om ons de beschikbare informatie ter beschikking ter stellen.
Bron: Motoklik.com
Tekst: Jens Köpke en Danny Hermans